Sterile Processing Departments (SPD) are some of the most complex and hard-working spaces within a hospital. The department cleans and sterilizes instruments and equipment for many inpatient and outpatient service lines, making it a constant hub of activity. They are critical to keeping a hospital and patient care operating safely and effectively and need to remain operational every hour of every day.
Renovation or expansion of a Sterile Processing Department is often a function of other growth needs within a hospital or may be a step in a series of moves to support a master planning effort. Expansion is typically needed to provide more processing equipment and increase throughput to accommodate growing surgery volumes. Updating the SPD space and equipment will improve workflows, safety, and quality.
In addition to improving workflows, safety and quality, Lean design tools can be used to develop a strategy for phasing to create a successful construction project. The following Lean Design tools actively involve stakeholders in the design process and leverage their ideas for improvement. This inclusion helps gather insights from various perspectives, ensuring the design meets the needs and preferences of those directly involved in the department’s operations.
Gemba Walk: Understanding Operational Challenges in Sterile Processing Departments
Initiating the project with a Gemba walk to observe current workflows and challenges is a key step. A Gemba walk – going to the place where the work is done – is an effective way to observe and understand current operations and any challenges. When performing a Gemba walk in the SPD, we follow staff, materials and instruments through the sterilization process to understand what is currently being done and look for opportunities to improve the process.
Complications with existing conditions such as department location, operational flows or staff movement need to be understood. The customers that Sterile Processing Department serve – hospital, outpatient or other offsite services – may dictate a need for more specialized plan solutions or scheduling of operations. In the case of a Sterile Processing Department serving an academic medical center, processing and sterilization of unique instruments used for research requires a dedicated workflow for the specialized sterilizing equipment.
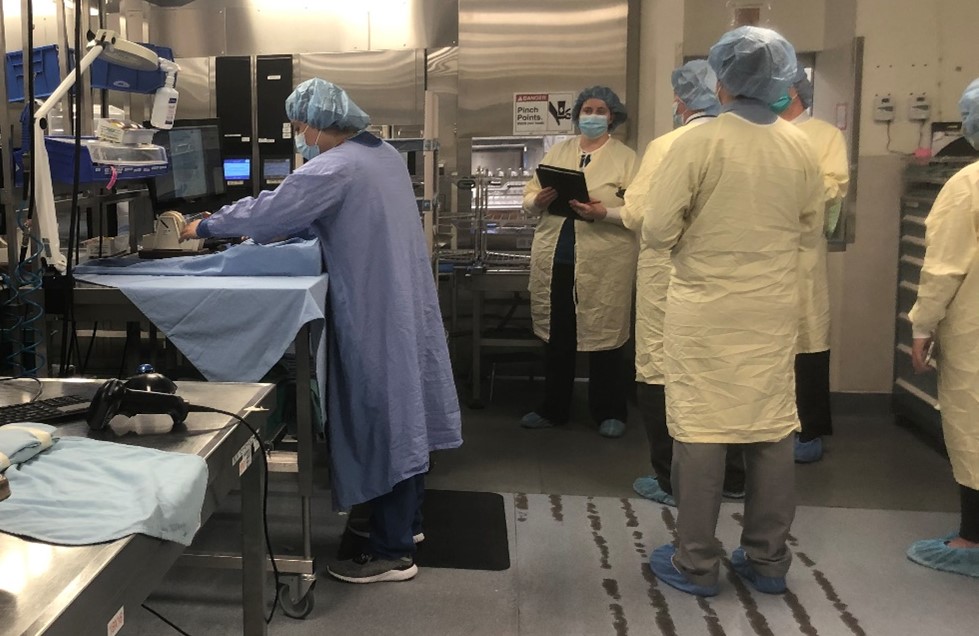
Leveraging Lean Tools to Engage Stakeholders
We use a Voice of the Customer exercise to identify the SPD customers and what is important to them. Customers can include staff who work in the department, clinical staff, facilities staff, support teams, leadership, and patients. This information helps the group develop the project goals. For a recent project at an academic medical center, the project goals we developed were:
- Incorporate the best practices for infection control and safety
- Improve staff efficiency
- Increase throughput and products for the department
Structuring design meetings as Kaizen (continuous improvement) events brings together stakeholders and consultants for collaborative decision-making. Staff can implement their improvement ideas when they participate in puzzle play exercises. In this collaborative design exercise, the design team and stakeholders use pieces to represent rooms and move them around on a floor plan. Puzzle play allows the team to quickly develop and test several different layouts. Each layout is evaluated on how well it meets the goals of the project – the Conditions of Satisfaction. Iterative review and testing ensure the optimum qualities of the different layouts are compared and synthesized, and a final layout is selected to be developed in further detail.
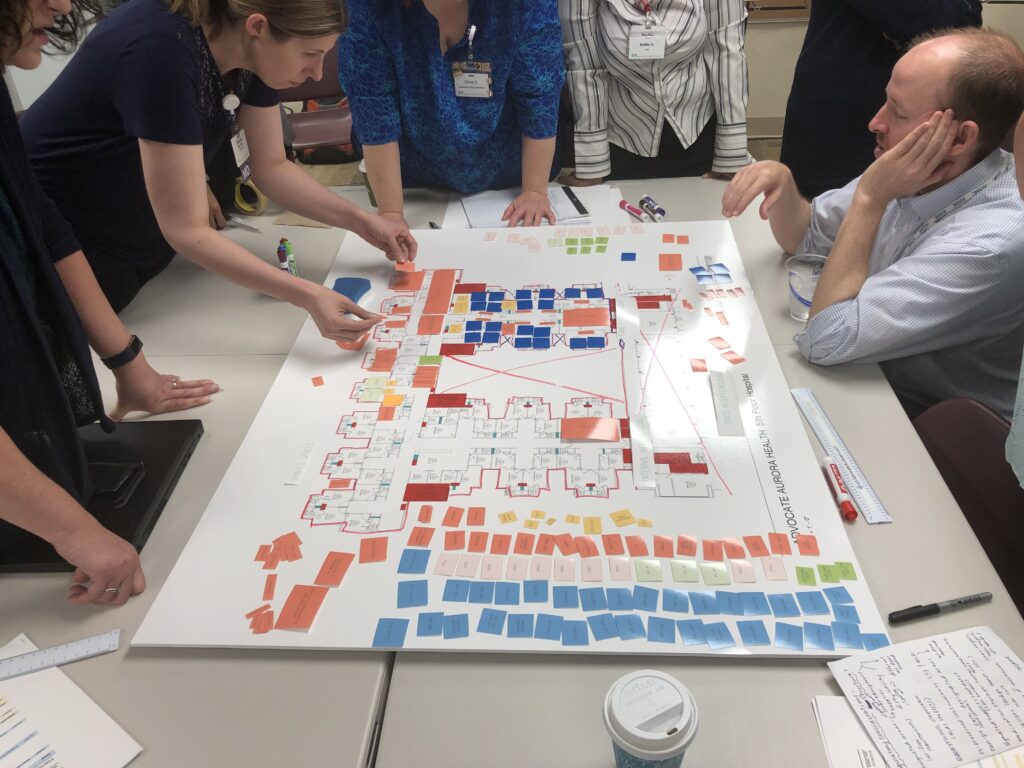
Create Flow and Pull to Improve Efficiency
Mapping current and future value streams to identify opportunities for workflow improvement is also a critical step in the Lean design process. The goal of value stream mapping is to create a system in which the products flow smoothly from the beginning of the process through delivery to the customer. This approach allows for a comprehensive understanding of existing processes and efficient planning for optimizations. A virtual whiteboard to map the current and future states can be used to allow everyone to visualize the processes. Identifying where delays and waste occur in the current state helps the stakeholders identify ways to make the future state more efficient and implement opportunities for improvement.
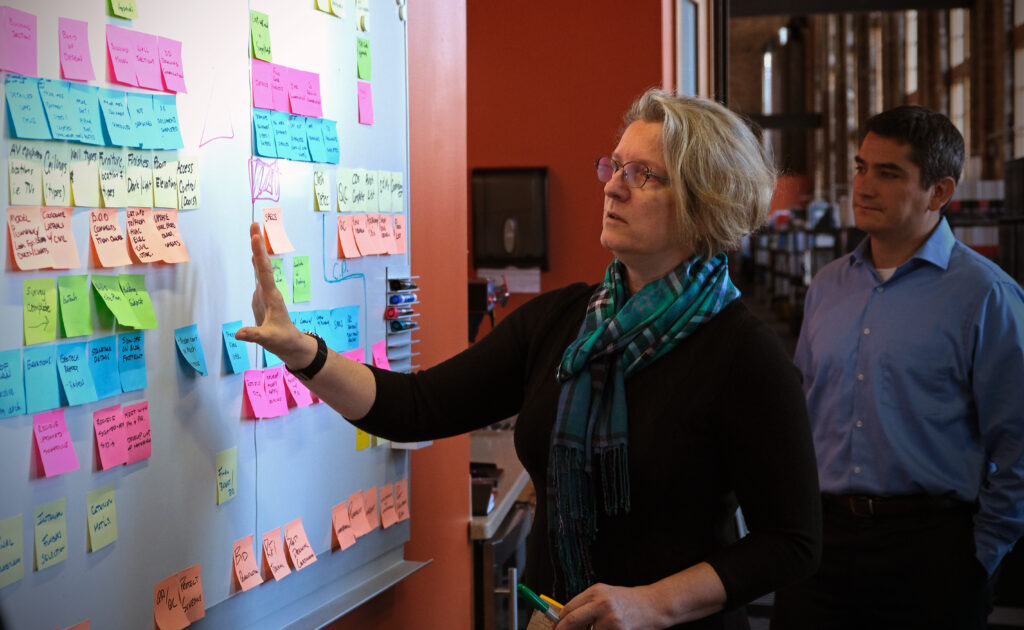
Optimizing Project Schedules through Collaborative Pull Scheduling
Pull schedule planning is utilized to identify bottlenecks and schedule impacts for the project. Pull schedule planning is a tool that engages the entire project team in developing the project schedule, with each member committing to milestones and deadlines. Long lead items, such as electrical and mechanical equipment and specialized sterile processing equipment, can be identified as drivers in the overall milestone schedule development.
A phasing approach can be developed to address the need to keep the department operational during construction. The design team and stakeholders then work collaboratively to develop a phased approach to construction in conjunction with developing the schedule. For a renovation or expansion, rarely is the phasing limited to just a few moves. In a recent renovation project, our team worked with the stakeholders and construction manager to develop a phased construction approach that used 9 phases keep the SPD fully operational. Involving the stakeholders in the phasing discussion was crucial to developing interim material delivery routes and staff flows
Lean Tools: Key to Streamlining Complex Project Delivery
Lean design tools identify and outline design challenges and determine opportunities for improvement. Through effective facilitation of this integrated Lean project delivery approach, our team works collaboratively with consultants and stakeholders to incorporate best practices for infection control and safety, improve staff efficiency, and increase throughput and productivity. This process is adaptable to all aspects of healthcare, but in this instance is uniquely tailored to solve the operational and construction phasing complexities of Sterile Processing Departments.